In this work, spark plasma sintering was applied for the consolidation of nano-sized Cu powders…
Microstructure investigation of spark plasma sintered nano-sized Cu powders
NGUYEN HOANG VIET, VU NGA LINH, NGUYEN THI HOANG OANH*
School of Materials Science and Engineering, Hanoi University of Science and Technology, Hanoi, Vietnam
*oanh.nguyenthihoang@hust.edu.vn
Ngày nhận bài: 18/7/2018, Ngày duyệt đăng: 27/9/2018
ABSTRACT
In this work, spark plasma sintering was applied for the consolidation of nano-sized Cu powders. The sintering process was performed at different sintering temperatures under pressure of 50 MPa with a heating rate of 50°C/min and holding time for 5 min. After sintering, all XRD patterns of samples sintered at 300, 400 and 500 oC showed diffraction peaks of Cu phase. At highest sintering temperature of 800 oC, besides peaks of Cu phase some small peaks belonging to Cu2O phase can be detected. The lattice parameters of sintered samples at 300, 400, 500 and 800 oC were 3.614, 3.618, 3.611 and 3.612 Å, respectively, which slightly different from the value reported in JCPDS 040836 file (3.615 Å). The hardness of the samples increased from 179 to 219 HV at the sin- tering temperatures of 300 and 400 oC, respectively. At higher sintering temperatures of 500 and 800 oC, the hard- ness values of samples decreased to 182 and 151 HV, respectively. The highest relative density of 94.5 % can be obtained for sample sintered at 400 oC. All samples fractured in a ductile mode.
Keywords: nano-Cu powder, spark-plasma sintering, TEM
TÓM TẮT
Trong công trình này, thiêu kết xung điện plasma được sử dụng để kết khối bột Cu kích thước nanô. Quá trình thiêu kết được thực hiện ở các nhiệt độ khác nhau với lực ép 50 MPa và tốc độ nâng nhiệt cao 50 oC/phút, giữ nhiệt trong 5 phút. Sau quá trình thiêu kết, các giản đồ nhiễu xạ tia X của các mẫu thiêu kết ở các nhiệt độ 300, 400 và 500 oC cho thấy các vạch nhiễu xạ của pha Cu. Ở nhiệt độ thiêu kết cao nhất là 800 oC bên cạnh vạch nhiễu xạ của pha Cu còn xuất hiện một số vạch nhiễu xạ nhỏ của pha Cu2O. Thông số mạng của các mẫu thiêu kết ở 300, 400, 500 và 800 oC tương ứng là 3,614; 3,618; 3,611 và 3,612 Å, các giá trị này có độ sai khác nhỏ so với giá trị nhận được trong thẻ JCPDS 040836 (3,615 Å). Độ cứng của các mẫu thiêu kết tăng từ 179 lên đến 219 HV tương ứng nhiệt độ thiêu kết ở 300 và 400 oC. Ở nhiệt độ thiêu kết cao hơn, tại 500 và 800 oC, độ cứng của mẫu giảm tương ứng là 182 và 151 HV. Tỷ trọng tương đối cao nhất nhận được là 94,5 % đối với mẫu thiêu kết ở 400 °C. Tất cả các mẫu phá hủy theo cơ chế phá hủy dẻo.
Từ khóa: bột nanô Cu, thiêu kết xung điện plasma, hiển vi điện tử truyền qua
1. INTRODUCTION
Copper (Cu) is widely used for electrical con- tact due to its high electrical and thermal conduc- tivities, low cost and good corrosion resistance [1]. However, poor mechanical properties of coarse- grained polycrystalline Cu such as low hardness and strength, narrow the range of its possible applications. In nanostructured materials, the large volume fraction of the atoms residing in the grain boundaries and small grain sizes, lead to an increase in strength and toughness of these materials [2-3]. The challenge to produce bulk samples over conventional sintering method to retained nanostructure of materials can be solved by Spark Plasma Sintering (SPS) technique [4-5]. During SPS, simultaneous application of the pressure and a rapid heating rate, by a pulsed electrical current with a DC bias voltage, helps in the densification without causing significant grain growth of nano- crystalline Cu. Zhang et al [6] SPSed the Cu nanoparticles prepared by the chemical reduction method of hydrazine hydrate with an average grain size of 50 nm. The grain size of Cu after sintering at 400 oC was about 180 nm. While Zhaohui et al. [7] using spherical Cu powder with an aver- age particle size of 1 µm for consolidation, grain size of copper after sintering at 400 oC was about 2.2 µm. By using different Cu particle size at the same sintering temperature, the grain size of Cu sample is also different which affected on the properties of bulk samples. In this work, Cu pow- ders with average particle sizes of 40 nm was used for starting materials. The densification of the sintered sample was discussed with reference to the SPS curve and effective sintering attained at various temperatures was evaluated by analyzing the fractured surface of the sintered samples.
2. EXPERIMENTAL
Copper powders with average particle sizes of 40 nm (US1090, US Research Nanomaterials, Inc.) were used as the staring materials. The sin- tering experiments were conducted using a SPS apparatus (DR. SINTER LAB Model: SPS-515S). The samples were heated from room temperature to 300, 400, 500 and 800 °C with a heating rate of 50 °C/min by pulsed DC current passing through the graphite die, punches and the sample itself. The samples were held at the sintering tempera- ture for 5 min. A pressure of 50 MPa was applied through the sintering process. The microstructure of the sintered samples was studied by Scanning Electron Microcopy (SEM) using a field-emission JEOL JSM-7600F microscope and Transmission Electron Microscopy (TEM) using a JEOL JEM-2100 microscope. The phase composition of the sintered samples was analyzed by means of X-ray diffraction (XRD) using RIGAKU RINT-2000 diffractometer with Cu Kα radiation. The relative density of the samples was determined by Archimedes’ method. The hardness of the samples was measured using a Vickers hardness instrument under a load of 100 g.
3. RESULT AND DISCUSSION
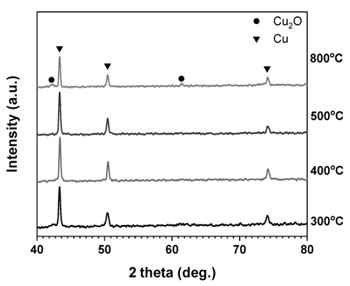
Fig. 1 shows the XRD patterns of samples were consolidated at different sintering temperatures. Only diffraction peaks of Cu phase can be detected for samples sintered at (300÷500) °C. At higher sintering temperature of 800 °C, beside peaks of pure Cu, small peaks belonging to Cu2O phase can be seen.
Based on the XRD results, the lattice parame ter of sintered samples, a, was determined by the relationship:
where dhkl is the interplanar spacing of (hkl) planes.
Table 1. Structural parameters of Cu for sample sintered at 300 °C
(hkl) | h2+k2+l2 | 2θ (°) | Sin θ | a(Å) | f(θ) | a(Å) from theNelson-Riley Plot |
111 | 3 | 43.359 | 0.369 | 3.613 | 2.379 | 3.614 |
200 | 4 | 50.480 | 0.426 | 3.615 | 1.952 | |
220 | 8 | 74.198 | 0.603 | 3.614 | 1.073 |
Table 2. Structural parameters of Cu for sample sintered at 400 °C
(hkl) | h2+k2+l2 | 2θ (°) | Sin θ | a(Å) | f(θ) | a(Å) from theNelson- Riley Plot |
111 | 3 | 43.400 | 0.370 | 3.610 | 2.376 | 3.612 |
200 | 4 | 50.520 | 0.427 | 3.612 | 1.950 | |
220 | 8 | 74.180 | 0.603 | 3.614 | 1.073 |
Table 3. Structural parameters of Cu for sample sintered at 500 °C
(hkl) | h2+k2+l2 | 2θ (°) | Sin θ | a(Å) | f(θ) | a(Å) from theNelson- Riley Plot |
111 | 3 | 43.360 | 0.369 | 3.613 | 2.379 | 3.611 |
200 | 4 | 50.461 | 0.426 | 3.615 | 1.953 | |
220 | 8 | 74.239 | 0.603 | 3.612 | 1.072 |
Table 4. Structural parameters of Cu for sample sintered at 800 °C
(hkl) | h2+k2+l2 | 2θ (°) | Sin θ | a(Å) | f(θ) | a(Å) from theNelson- Riley Plot |
111 | 3 | 43.360 | 0.369 | 3.613 | 2.379 | 3.612 |
200 | 4 | 50.499 | 0.426 | 3.613 | 1.951 | |
220 | 8 | 74.218 | 0.603 | 3.613 | 1.072 |
Table 5. Crystallite size of Cu for sample sintered at 300 °C
2θ | FWHM-B (o) | Crystallite size (nm) | Average crystallite size (nm) |
43.359 | 0.287 | 31.125 |
3.6 |
50.480 | 0.472 | 19.442 | |
74.198 | 0.510 | 20.403 |
The values of the interplanar spacing and lattice constants of Cu are reported in Tables (1-5). The corrected values of lattice parameter are estimated from the Nelson-Riley extrapolation method [8-9]. The values of the lattice parameter obtained from each reflected plane are plotted against the Nelson-Riley function f (θ):
where θ is Bragg’s angle. The value of the lat- tice parameter was estimated by extrapolating the straight line to = 0. The lattice parameter of Cu was 3.614, 3.612, 3.611 and 3.612 Å for samples sintered at 300, 400, 500 and 800 °C, respectively. These values are slightly different from the value reported in the Joint Committee on Powder Diffraction Standards JCPDS 040836 file (3.615 Å).
According to Scherrer equation, the values of crystallite size of copper are calculated from para- meters of the three most intense peaks (described by Miller indices-h, k, l) of copper phase:
where:
L – Average crystallite size (nm), K – Scherrer constant, K = 0.94 for spherical crystallites with cubic symmetry, λ – X-ray wavelength for Cu Kα l = 1.54178 Å, B – FWHM (Full Width at Half Maximum) of XRD peak, θ – XRD peak position, one half of 2θ.
The crystallite size of Cu increases from 23.6 to 30.4 nm for samples sintered at 300-800 °C (table 5-8).
Table 6. Crystallite size of Cu for sample sintered at 400°C
2θ | FWHM-B (o) | Crystallite size (nm) | Average crystallite size (nm) |
43.360 | 0.274 | 32.602 |
27.2 |
50.461 | 0.343 | 26.752 | |
74.239 | 0.465 | 22.384 |
Table 7. Crystallite size of Cu for sample sintered at 500°C
2θ | FWHM-B (o) | Crystallite size (nm) | Average crystallite size (nm) |
43.400 | 0.268 | 33.336 |
29.1 |
50.520 | 0.318 | 28.863 | |
74.180 | 0.411 | 25.315 |
Table 8. Crystallite size of Cu for sample sintered at 800°C
2θ | FWHM-B (o) | Crystallite size (nm) | Average crystallite size (nm) |
43.360 | 0.231 | 38.670 |
30.4 |
50.499 | 0.330 | 27.811 | |
74.218 | 0.418 | 24.897 |
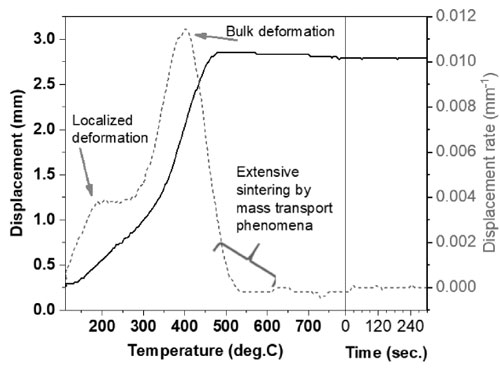
Fig. 2 presents the displacement and displace- ment rate versus sintering temperature. The shrinkage of sample increases from room temperature to 475 °C. The highest shrinkage can be seen at 475 °C, then keep stable during holding time. This tendency can be °C curred when sintering atomized Cu powders [10]. The displacement rate shows two peaks: a weak peak at 200 °C and a broad peak with the maximum displacement rate at 400 °C. Hu Wang [11] also reported three peaks in the curve of punch displacement rate with time during sintering of silver powder at 500 °C. It is explained that the first peak appeared due to the release of gases in powder. And the second peak is the formation and growth of necks. Then, the highest peak III can be observed when the sinter ing pressure is applied. In this work, to interpret the second peak from displacement rate curve as shown above, samples were broken to observe the fracture surface which are reported in Fig. 3a. The fracture surface of the sample sintered at 300 °C displays some necks and the absence of a duc- tile fracture morphology indicate that sintering phenomenon is responsible for the formation of metallic bonding between particles [12]. At higher sintering temperature of 400 °C the Fig. 3b illus- trates a dimpled fracture indicative of an effective consolidation of the material. It may be concluded that mass transport phenomenon responsible for neck formation and growth mainly °Ccurs between 300 and 400 °C. The two peaks of the displace- ment rate curve can be attributed by the following phenomena: localized deformation at the contact points and core deformation. The particle size of copper increases from a few hundred nanometers to several micrometers (Fig. 3c,d) as increasing temperature from 500 to 800 °C which was report- ed in reference [7].
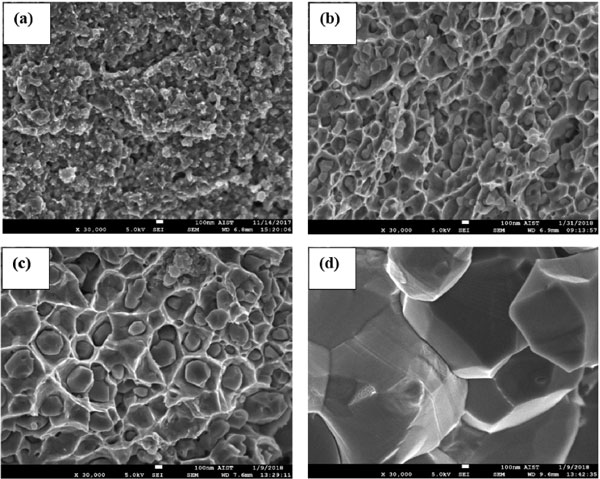

Fig. 4 depicts the microstructure images of the Cu sample sintered at 400 °C observed by HR- TEM. The average grain size of copper was about 30 nm which is consistent with XRD calculation in table 6.
The relative density of the samples sintered at different temperatures are shown in table 9. At the beginning the sintering process at 300 °C, the rel- ative density of sample is about 77.43 %. The dis- charge effect, the Joule heat and the plastic defor- mation under pressure are main factors for densi- fication of the copper powders. The density improves significantly to 94.5 % at sintering temperature of 400 °C, the distance between particles reduces remarkable, the discharge effect weakens due to the current passes through these particles directly. The joule heat and the plastic deformation under pressure become the main factors for densification. At higher temperature of 500 °C, the rel- ative density values decrease due to grain growth of copper. Zhao-Hui Zhang et al. [7] sintering ultrafine copper at the same sintering temperature have the relative density of the bulk compact of 77.46 %. The different size of starting Cu powders results in different sintering behavior. The hard- ness of bulk samples reported in Table 10 is in agreement with the density data due to the presence of porosity at low sintering temperature of 300 °C. A highest hardness value is 219 HV can be obtained for sample sintered at 400 °C. The hardness of bulk samples decreases at higher temperature of 500 and 800 °C due to the lower relative density (Table 9) and grain growth (Fig. 3).
Table 9. Relative densities of sintered copper samples
SPS temperature (oC) | 300 | 400 | 500 | 800 |
Relative density (%) | 77.4 | 94.5 | 93.0 | 78.1 |
Table 10. Hardness values of sintered copper samples
SPS Temperature (oC) | 300 | 400 | 500 | 800 |
Hardness (HV) | 179 | 219 | 182 | 151 |
CONCLUSIONS
In this work, the nanostructure of Cu samples was produced by an SPS technique. The highest relative density and hardness value can be obtained for sample sintered at 400 °C is 94.5 % and 219 HV, respectively. The sintering tempera- ture has a significant effect on grain size of bulk samples. The crystallite size of Cu increases from 23.6 to 30.4 nm for samples sintered at tempera- ture range of 300÷800 °C. The average grain size of sample sintered at 400 °C calculated from XRD pattern and observed by HRTEM is about 30 nm. At higher sintering temperature of 500 °C, the rel- ative density and hardness value decrease to 93 % and 182 HV, respectively. The grains grow significantly and the average grain size of Cu increases about several micrometers at 800 °C. A dimpled fracture morphology was observed for sintered samples.
REFERENCES
- Joseph R. Davis, ASM specialty handbook: Copper and Copper Alloys, ASM International, 2001.
- C. Suryanarayana and C. C. Koch; Nanocrystalline materials-Current research and future directions, Hyperfine Interactions, 130, 2000, pp. 5-44
- Y. M. Wang, E. Ma; Three strategies to achieve uniform tensile deformation in a nanostructured metal, Acta Materialia, 52, 2004, pp. 1699-1709.
- C. Menapace, G. Cipolloni, M. Hebda, G. Ischia; Spark plasma sintering behaviour of copper powders having different particle sizes and oxygen contents, Powder Technology, 291, 2016, pp. 170-177.
- S. Diouf, C. Menapace & A. Molinari; Study of effect of particle size on densification of copper during spark plas- ma sintering, Powder Technology, 291, 2016, pp. 170-177.
- Z. H. Zhang, F. C. Wang, S.K. Lee, Y. Liu, J. W. Cheng, Y. Liang; Microstructure characteristic, mechanical prop- erties and sintering mechanism of nanocrystalline copper obtained by SPS process, Materials Science and Engineering A, 523, 2009, pp. 134-138.
- Zhang Zhaohui, Wang Fuchi, Wang Lin, Li Shukui, S. Osamu; Sintering mechanism of large-scale ultrafine- grained copper prepared by SPS method, Materials Science and Engineering A, 476, 2008, pp. 201-205.
- Cullity BD, Elements of X-ray Diffraction, Addison-Wesley, Reading, Massachusetts, 1979.
- O. M. Lemine, Effect of milling conditions on the formation of ZnFe2O4 nanocrystalline, International Journal of Physical Sciences, Vol. 8 (10), March 2013, pp. 380-387.
- G. Cipolloni, M. Pellizzari, A. Molinari, M. Hebda, M. Zadra; Contamination during the high-energy milling of atomized copper powder and its effects on spark plasma sintering, Powder Technology, 275, 2015, pp. 51-59.
- Hu Wang, Microstructures and mechanical properties of bulk nanocrystalline silver fabricated by spark plasma sintering, JMR journal of materials research, Volume 31, Issue 15, 2016, pp. 2223-2232.
- Oanh Nguyen Thi Hoang, Viet Nguyen Hoang, Ji-Soon Kim, and Dina V. Dudina; Structural Investigations of
- TiC-Cu Nanocomposites Prepared by Ball Milling and Spark Plasma Sintering, Metals, 7 (4), 2017, id. 123.